Managing food product specifications is no small feat. From navigating compliance to ensuring quality, modern food product management demands can be tough to keep up with — especially if you're trying to do it with tools that have passed their shelf life. So, how can you tell if your food product specification management have gone stale? If any of the signs below sound familiar, it might be time to consider a fresh solution that simplifies, centralizes, and supports your product specification management process better.
Your Competitors Keep Beating You to Market
If you feel like you’re playing catch-up with competitors even when your team is consistently innovating, it could be a sign that your current processes are slowing you down. If you're is bogged down by manual workflows and data entry, your product development cycles can feel like they’re moving much more slowly than they should. Speed to market is crucial in the food industry, and having outdated systems can hold you back, letting competitors get that valuable first-mover advantage.
Read More: How to Increase Your Speed to Market for New Recipes & Food Products
Another factor could be the way your team collaborates. Even when no one is gatekeeping information, data siloes can crop up gradually and lead to miscommunication between departments and unclear approvals, slowing progress and holding back go-to-market plans. It's hard to turn ideas into action when everyone isn’t on the same page, so a streamlined, connected system that keeps everyone in sync can make all the difference in getting products out the door faster and more efficiently.
You’re (Still) Struggling with Regulatory Compliance
Staying compliant with food safety and labeling regulations can feel like a never-ending task, especially when the rules keep evolving. Regulations on allergens, labeling, and food safety protocols can vary widely depending on the region, and it can be exhausting to keep track of each detail manually. Falling behind on compliance isn’t just risky for consumers — it can lead to costly recalls, fines, and a hit to your brand’s reputation that’s hard to recover from.
Listen Up: Traceability, Consumer Trust, and Kroger's Approach to FSMA 204
Even for teams that stay on top of each and every regulatory update, managing compliance documentation can be an outsized drain on resources. If you’re juggling certifications, audit trails, and supplier records across different platforms or spreadsheets (or worse, paper files), it’s easy for something to slip through the cracks. A product management solution that centralizes and organizes everything you need to achieve compliance can help you stay on top of new and existing requirements, safeguard your customers and brand, and reduce the chance of actions or penalties.
Sourcing Ingredients Without Sacrificing Quality is a Challenge
Keeping up with supplier quality and consistency isn’t always easy, especially when you’re fostering relationships with multiple vendors. If you’re struggling to track supplier performance, certifications, and compliance records, you meed a better solution. Without a reliable way to manage these details, it can be challenging to ensure that your ingredients are meeting your quality standards—and that can ultimately impact the final product on the shelf.
Digital Download: The Supplier Relationship Management Playbook
There are the daily challenges that come with supplier relationship management, and then there are major supply chain disruptions. Needing to manage logistics challenges has always been a reality for food companies, but the past decade has been a lesson in needing to be as agile and resilient as possible. Even when you can anticipate them, delays, shortages, and other disruptions can quickly throw off even the best laid plans.
When food supply chain systems aren’t built to adapt and respond to these issues, food companies are left scrambling. A solution that provides visibility and accountability across your supplier network can help you respond to challenges faster and keep quality intact.
You’re Stalling When You Should be Scaling
When you’re ready to grow, you want systems that can grow with you. But if your processes are manual and spread across disparate systems and platforms, scaling up means more time, more work, and more room for errors. As your product range expands, managing the complexity with spreadsheets and fragmented systems will lead to more bottlenecks and mistakes.
Case Study: How Tyson Uses FoodLogiQ to Connect Its Supply Chain
Growth is great, but it also introduces new layers of complexity. You may have multiple product variations, different production facilities, and a broader set of compliance requirements to manage. Without the right support, the risk of errors and inconsistencies increases, which can lead to quality issues or even product recalls. A system built for scalability can help you streamline these processes, giving you the room to grow without the growing pains.
Stale Data Results in Half-baked Decisions
Making decisions based on old or incomplete data is like driving with a foggy windshield; you can either go slowly and arrive late or take unnecessary risks to make better time. When it takes too long to pull together accurate data on product performance, ingredient costs, or supply chain trends, you can't make timely, informed choices. Outdated data can prevent you from spotting issues early or responding to trends, which limits your ability to innovate and stay competitive.
Listen Up: How AI Can Transform Food Safety
A lack of real-time data also hampers your ability to track and improve performance. You might have a hard time identifying areas where costs could be optimized or where processes could be streamlined. Having timely, accurate data at your fingertips can empower your team to make proactive decisions and seize new opportunities before they pass you by.
You’re Making Do with Manual Processes
If you’re still relying on paper forms, spreadsheets, and manual data entry, it’s no wonder if you’re feeling the strain. Manual processes are more than slow and tedious; they also leave plenty of room for error. Mistakes in product specs, ingredient tracking, or compliance documents can lead to costly setbacks, food safety and quality assurance headaches, and even withdrawals.
The lack of visibility that comes with scattered data sources is another drawback of manual processes. When each department has its own records and systems, it’s tough to get a clear, centralized view of product information and supply chain data. A digital, centralized solution can help teams work together seamlessly, improving accuracy and freeing up time for what really matters.
The Missing Ingredient: FoodLogiQ’s Product Management Solution
If these challenges are all too familiar, then it might be time to explore a solution made specifically for food businesses: FoodLogiQ’s Product Management software.
Designed to simplify, streamline, and support every aspect of food product specification, FoodLogiQ’s platform brings your product information, compliance needs, and collaboration workflows together in one easy-to-manage space.
Streamlined Specification Creation & Management
FoodLogiQ makes creating and managing product specifications straightforward and efficient. With over 100 built-in attribute options and customizable fields, you can develop product specs that fit your business exactly—whether it’s tracking ingredients, nutritional info, or supplier details. If you’re producing multiple variations of a product, you can manage everything from a single template.
Centralized Product Specification Management
Bring everything you need into one central platform. With a Genesis Foods integration, you can easily access nutritional data, allergen information, and ingredient lists without having to re-enter data or cross-check different tools. All of your team members—from R&D to compliance—can tap into a single source of truth.
Internal Collaboration & Compliance Approvals
FoodLogiQ helps keep everyone on the same page. With built-in workflows, you can route specifications to legal, accounting, and food safety teams for approvals. This makes it easy to track who’s signed off and when, while providing an audit trail for internal reviews or external audits, giving you full transparency and peace of mind.
Facility-Level Approval and Variance Management
Scaling production? No problem. FoodLogiQ lets individual manufacturing facilities acknowledge or reject product specifications based on their unique needs, with all decisions linked back to a master specification. This setup ensures that your facilities maintain consistent quality standards, while still allowing for local adjustments when needed.
Integrated Nutrition Spec Sheet Data
Thanks to Genesis Foods integration, you can automatically pull in precise nutritional information, allergen statements, and ingredient lists for each product spec. This not only helps keep your labels accurate, but it also reduces the risk of costly allergen-related mistakes. As you tweak or update formulations, FoodLogiQ Product Management syncs these changes, so you’re always confident that your product labels are up to date and compliant with current regulations.
Refresh Your Food Product Specification Management System
You don’t have to keep relying on systems that aren’t keeping up with your company's needs. FoodLogiQ’s Product Management software is designed to tackle challenges just like these that food companies face everyday. From ensuring compliance and speeding up approvals to streamlining supplier communication and enhancing collaboration, FoodLogiQ is purpose-built to help you stay agile and competitive in a fast-paced market.
Access the latest product specs, nutritional data, and supplier details seamlessly with FoodLogiQ, and move forward with new products that meet your standards for quality and compliance. Ready to see how FoodLogiQ can transform your product management? Contact Trustwell today or try an interactive demo of FoodLogiq Product Management and discover for yourself how our solution can support your business, from recipe to recall.
Tag(s):
Food Industry
Other posts you might be interested in
View All Posts
Food Industry
6 min read
| October 18, 2019
5 Ways You Can Build a Brand on Food Safety
Read More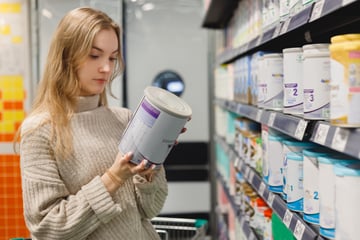
Food Industry
11 min read
| March 31, 2023
Three Takeaways from the 2021-2023 Infant Formula Recalls and Shortages
Read More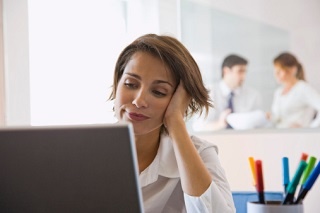
Food Safety
6 min read
| June 23, 2016