The FDA’s public meeting held in October, 2019 highlighted the need to bring both public and private industry partners together. It will take tremendous collaboration to advance a New Era of Smarter Food Safety at scale. Public dialogue around food safety and traceability is essential to accomplish the goals of this new campaign, which will be people-led, FSMA-based, and technology-enabled. To contribute to public discourse, FoodLogiQ has formally submitted comments on the initiative, read the full version of our statement here.
Companies understand there are many drivers moving them to become more transparent. One of the challenges is engaging all parties to participate in order to facilitate end-to-end traceability and transparency. This will require new ways of doing business, changing internal and external processes, and embracing innovative approaches to collecting product data, including the adoption of new technologies.
We commend the FDA’s approach that smarter food safety should be driven by people, in tandem with regulation and the adoption of technology. At FoodLogiQ we have helped shape policy at the national level, assisting in the definition of the Produce Traceability Initiative standards and were one of the FDA’s traceability pilots that shaped regulation of the Food Safety Modernization Act. We have worked hand-in-hand with the food industry’s leading innovators to develop our traceability solutions. And because we only work with the food industry, we have developed our software solely to meet the unique needs of the food supply chain.
The FDA and industry partners rely on supply chain information in order to protect consumers. Trace back and trace forward investigation data needs to be readily available, and most importantly, understandable across the supply chain. GS1 Standards, which were created by industry stakeholders, have been in place for many years. To date, the adoption and use of these standards has been driven by end users such as grocery retailers and foodservice operators. Most supply chain partners adopted the standards because of these trading partner mandates, and even then, adoption often is not corporate-wide. In our experience, many companies struggle to meet the minimum requirements for these trading partner mandates. This needs to change.
FoodLogiQ supports some of the largest foodservice operators, food manufacturers and grocers in the world. This provides us with a unique perspective regarding the challenges and opportunities facing food industry partners when implementing traceability programs. Representatives from various companies have told us they will not participate unless it is a government requirement. Other companies struggle when their various trading partners have competing, and sometimes conflicting, requirements.
Key Data Elements (KDEs) and Critical Tracking Events (CTEs) are being used effectively today, providing real-time traceability, as long as companies do not attempt to create their own system or standard. This slows adoption, adds cost and makes it almost impossible to comply with every partner’s mandate.
It is paramount to outline expectations and guidelines for compliance: guidance from the FDA will need to cover many areas. For traceability, the following should be considered:
- Define KDEs required for each CTE.
- Standardize product attribute definitions and code lists.
- Create a standard taxonomy or nomenclature for common industry terms in order to standardize data submittal.
- Use globally unique product and location identifiers.
- Set clear expectations for product identification at each level of the hierarchy.
- Create unique identification of each company and their physical locations.
- Define the minimum set of CTEs needed for an FDA investigation.
- Provide guidelines regarding interoperability, regardless of technology platform.
- Recommend a standard, electronic format to share investigation data with the FDA.
As we move forward, companies need to adopt technology that offers precision and accuracy where it’s needed most. They need tools to communicate across supply chains to prevent tainted or poor quality products from being delivered to consumers and proactively implement corrective actions before major issues arise.
There are many solutions in place today that enable companies to achieve end-to-end traceability. These include a range of technologies such as: Artificial Intelligence (AI), Internet of Things (IoT), Machine Learning (ML), cloud-based services (i.e. SaaS), and distributed ledgers (i.e. blockchain), all of which achieve an unparalleled level of supply chain reporting and insights. However, these technologies are inoperable if the data is not standardized, normalized and harmonized. Users need a common set of attributes and data loading options. Solution providers also need a common format so they can communicate with one another.
Our vision for the world is a connected food chain where technology drives transparency, consumers can get the information they want about the food they love, there are fewer food recalls and most importantly, fewer lives lost due to foodborne illness. We work alongside our customers to shape the roadmap of our software, FoodLogiQ Connect, focused on this vision.
Read or download the entirety of FoodLogiQ’s public comments on regulations.gov.
Other posts you might be interested in
View All Posts
Traceability
10 min read
| February 25, 2021
FoodLogiQ Commentary on the FDA's FSMA 204 Proposed Rule
Read More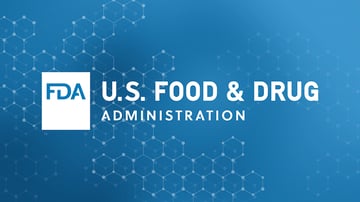
Food Safety
10 min read
| December 6, 2021
FoodLogiQ Comments: New Era of Smarter Food Safety Summit on E-Commerce
Read More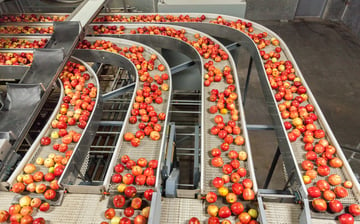
Trustwell News
6 min read
| December 17, 2021