Last week, Consumer Reports announced that, in light of the recent series of foodborne illness outbreaks linked to leafy greens, the publication had conducted its own testing of 284 samples of leafy greens purchased from various retailers. The results from those tests showed Listeria monocytogenes were present in six of the samples. These findings are now being reviewed by the Food and Drug Administration.
Consumer Reports Testing Results
- Of the samples testing positive for listeria, two of the greens were pre-washed and packaged, and the other four were loose heads or bunches.
- The packaged items were spinach and an organic spring mix with spinach, and the bulk products were green kale, green leaf lettuce, red leaf lettuce and spinach.
- According to the publication, one of the samples that tested positive for listeria had a strain genetically linked to two illnesses that had been reported to the Centers for Disease Control and Prevention (CDC). Consumer Reports says that finding led the FDA to perform an inspection at the processing facility.
The FDA Responds
“We continue to look at the data provided by Consumer Reports,” says FDA press officer Peter Cassell. “The FDA takes the presence of harmful pathogens in our food supply very seriously and considers the risk to public health when taking action.”
In response to the Consumer Reports leafy greens testing and subsequent findings, the FDA states that it, “...continues to recommend that leafy green growers, buyer/shippers and retailers be able to trace product back to the specific source in real time and make information about the source, such as harvest date and standardized growing regions, readily available for consumers.”
Demand for Traceability is High
“From our perspective, the FDA’s recommendation is not just a nice-to-have for the stakeholders throughout the supply chain - it’s a must-have,” says Katy Jones, Chief Marketing and Strategy Officer at FoodLogiQ. “Yes, it’s true that food recalls are a fact of life, and they can happen for a variety of reasons. However, consumers have high expectations when it comes to the timing of a recall or withdrawal. Our research shows they believe a recall should be executed within 24 to 48 hours. That is extremely difficult to achieve if you don’t have technology that enables seamless communication across supply chain partners supported with whole-chain traceability.”
When retailers are faced with a recall, they must be able to quickly remove that product out of their locations in order to protect their customers. FoodLogiQ Connect’s Recall + Response enables organizations to streamline that process and to ensure an effective and efficient chain of events. Using Recall + Response, food companies can:
- Define workflows for withdrawals based on your company’s unique process
- Create a continuous flow of information about the recall throughout the entire supply chain via text, email and phone
- Build automatic escalation if no action is taken by a location or individual within a specific timeframe
- Monitor the recall or stock withdrawal in real-time via a live dashboard
- Target a recall or withdrawal on specific products or locations within your supply chain
- Have complete documentation on the results of the recall or withdrawal once it is resolved
“Food safety management is a complex process, but with the right technology, organizations can respond to recalls with speed and accuracy,” Jones says.
To learn how you can have confidence responding to a recall or withdrawal, request a demo.
Other posts you might be interested in
View All Posts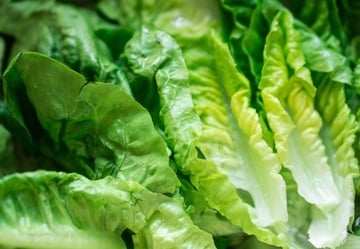
Food Industry
6 min read
| September 3, 2019
A Year Later: What We Learned About the 2018 Romaine Lettuce Recall
Read More
Industry Regulations
10 min read
| March 13, 2020
The FDA's Leafy Greens Action Plan
Read More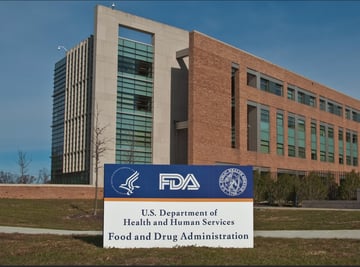
Food Industry
7 min read
| October 9, 2018