Learn about the role food quality assurance plays across the industry, as well as the importance of adopting digitized methods in support of the future of traceability.
While quality assurance (QA) is an indisputably vital factor across industries and their respective supply chains, it is of utmost importance within the food supply chain. Food quality assurance consists of a series of practices utilized by food and beverage companies to guarantee that their products are meeting industry, brand and consumer standards, in addition to safety regulations. In turn, these practices generate consumer trust, allowing customers to develop confidence in these brands and their ability to satisfy quality requirements, as well as generate products that are safe for consumption.
It’s important to note, however, that external bodies, such as individual customers, regulatory and governmental agencies, are not the only ones who benefit from strong food quality assurance practices. In instituting an active, trusted QA process, brands and their employees ensure, and thus rest assured, that their products are safe and satisfying to the public. Additionally, customers are more likely to repeatedly purchase products and develop strong brand loyalty when they know that the food in question exceeds all safety and quality measures.
Food quality assurance practices may include process checklists, documentation, audits and assessments, among other testing and preventive measures. Such protocols are essential for meeting brand standards and regulatory requirements, including those featured in the FDA’s Food Safety Modernization Act (FSMA). In addition, they enable the world’s biggest and most impactful food and beverage companies to generate consumer trust, drive brand loyalty and expand their customer base. The FoodLogiQ Connect platform makes all of these processes easier, smoother and more scalable through digital quality assurance and incident management.
Food Quality Assurance and the Future of Traceability
In November of 2022, the FDA will finalize Section 204 of the Food Safety and Modernization Act (FMSA), at which point businesses will be required to start complying with the new rule. FSMA 204 will essentially enable tracking at every step in the supply chain, beyond what is required according to FSMA today. This affects those who manufacture, process, pack and hold foods on the FDA’s Food Traceability List (FTL). The foods that are included in this rule cover a wide group of items, such as cheeses, fresh-cut fruits and vegetables, nut butters, produce, ready-to-eat deli salads, seafood and shell eggs. In addition, the proposed ruling applies to foods that appear on the FTL and act as ingredients in other final products. For example, crackers containing nut butter would also be subject to the proposed requirements.
According to the proposed traceability rule, records must be maintained as original paper records, electronic records or true copies, and must be stored for 24 months. Additionally, if information is requested by the FDA, this data must be reported within a 24-hour time frame. As a result, the need for a centralized, consolidated digital record is paramount.
FSMA 204 is not only part of a comprehensive food safety assurance program; it represents a huge step towards the future of traceability within the food industry. And while staying proactive in meeting standards and other processes in food quality assurance may sound overwhelming, FoodLogiQ makes things run in a smooth, organized fashion.
Tech-Enabled Food Quality Assurance
FoodLogiQ’s Manage + Monitor platform allows companies to centralize their supplier management, compliance and quality management processes, enabling a high level of visibility across the supply chain and empowering fortified food quality assurance programs. Manage + Monitor diminishes unnecessary communication time, and allows businesses to build trusted, ongoing relationships with their suppliers through centralized, direct communication, clear expectations and enhanced usability. In short, with FoodLogiQ Connect, everything that you need to know about your supply chain is in one location.
The quality incident management tool within Manage + Monitor allows for constant monitoring and enhanced data visibility, on both the individual incident and collective trendline levels. Food and beverage brands can attain granular data on quality incidents, their locations and the products involved, as well as utilize Reports to uncover and reduce incident commonalities by date, location and type.
As a result, users can capture food quality issues in real-time from anywhere across the supply chain, understanding exactly what risks exist, which locations are affected, and what steps are necessary for taking immediate action. With Manage + Monitor, it’s easy to communicate quality incident details and action items directly to suppliers, as well as issue and recoup credit – all from one centralized space.
Across the food industry, FoodLogiQ’s Manage + Monitor software makes the fast-growing future of food quality assurance accessible, central and simple, leading to a safer, healthier tomorrow. To learn more about how to effectively and efficiently manage your quality assurance processes, as well as prepare for FSMA 204 compliance, reach out and schedule some time with us.
Other posts you might be interested in
View All Posts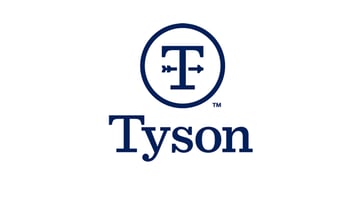
Quality Management
5 min read
| August 23, 2018
Tyson Foods Selects FoodLogiQ to Connect Supply Chain
Read More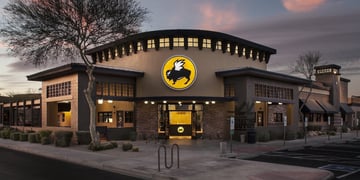
Food Industry
5 min read
| May 14, 2018
Supply Chain Visibility a Key Challenge Throughout Food Industry
Read More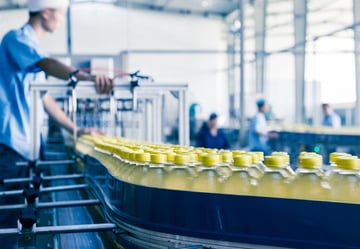
Supplier Compliance
6 min read
| August 16, 2019