Food recalls. It’s rare for a day to go by when one isn’t announced. Large or small, mandatory or voluntary, food recalls come in all shapes and sizes, but they all have one thing in common - they are a major disruption to your company’s supply chain.
A recent study by a professor at the University of Notre Dame found that being able to trace a product through the supply chain is critical to quickly locating and removing bad products during a food recall. Yet many companies are struggling with implementing food traceability systems.
We sat down with the study’s lead author, Dr. Kaitlin Wowak, assistant professor of management at Notre Dame’s Mendoza College of Business, to talk more about the benefits of end-to-end traceability for effectively managing food recalls.
“Tracing Bad Products in Supply Chains,” recently published in the Journal of Business Logistics by Wowak (pictured left), outlines the need to manage traceability from a nuanced approach. “We saw many companies who treat traceability as a ‘one-size-fits-all’ for their supply chain, and that’s really not the way to look at it,” said Wowak.
“Perishable products, like fresh produce and meats, flow through the supply chain very quickly. And while federal regulations mandate that firms have traceability one step up and down the chain, this may not be sufficient for these perishable products. In those situations, there is often a gap in the information received about the product, say a positive Listeria test, and where that product went in the supply chain.”
This is precisely why Wowak stresses the importance of end-to-end traceability.
“Having traceability two or three steps up and down the entire supply chain is an absolute must for companies who want to handle recalls better. This really allows you to act faster and with more precision when recalling product.”
And Wowak found that traceability can benefit a company’s bottom line on top of its food safety practices.
“We talked to companies who, when faced with a recall, pulled product out of their supply chain and only 50 percent of that product was actually tainted. The other 50 percent was perfectly fine. That gets really expensive for the company, not to mention contributing to the mounting issue of food waste. But they don’t have a choice without the visibility that end-to-end traceability allows.”
Wowak’s advice for companies implementing traceability? Go beyond the “one-up-one-back” requirement under the Food Safety Modernization Act. “I’m sure we are going to get more regulations in the future, so going above and beyond now will just make you even more prepared for the future.”
Wowak also stresses the importance of implementing a traceability system that works to break down barriers across a company and opens up a dialog about transparency.
“Companies with best-in-class traceability are the ones who are able to minimize the damage to their brand once a product recall has occurred,” said Wowak. “These are the companies where you see an understanding of food traceability systems across the organization. They view their suppliers much more as partners, not as much solely as a business transaction.”
And while recalls continue to be on the rise, Wowak is hopeful for the future of the food supply chain.
“Companies are really taking traceability more and more seriously. It is amazing to see how transparency can really align an organization through their supply chain.”
Effectively managing food recalls requires end-to-end traceability. Take a step toward supply chain visibility with our free guide, Selling the C-Suite on Supply Chain Traceability Software.
Tag(s):
Traceability
Other posts you might be interested in
View All Posts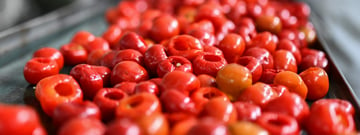
Food Safety
6 min read
| October 14, 2022
Modern Traceability Recordkeeping, FSMA 204, and the Supply Chain
Read More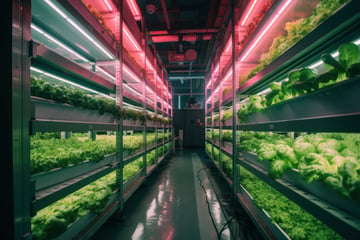
Supplier Compliance
9 min read
| August 24, 2023
Lessons Learned from Major U.S. Recalls & How Traceability Tech Turns the Tide
Read More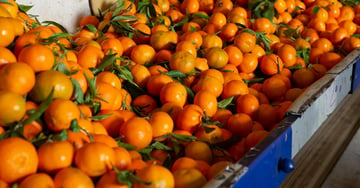
Food Safety
5 min read
| January 24, 2023