FoodLogiQ’s new E-Book, “The Food Manufacturer’s Guide to Effective Product Removal Management,” details methods for executing product removal processes and preventive strategies. Access it now.
Product removals, withdrawals and recalls happen a lot. And they continue to rise in number across the industry. According to a report released by the Public Interest Research Group (PIRG), the total number of food recalls in the U.S. increased by 10% between 2013 and 2018, reaching an impressive 905 in 2016. The report details that meat and poultry incidents rose by 67% during this time period. In addition, Class I recalls, or those in which there is reasonable probability that product consumption or exposure will cause serious health consequences, of meat and poultry increased by 83%.
And while only a small fraction of these product removals make it to the eyes and ears of consumers via media coverage, the pervasiveness of these events doesn’t make them any less damaging.
According to the Grocery Manufacturers Association’s report Capturing Recall Costs:
- 81% of respondents deem financial risk from recalls as significant to catastrophic
- 58% have been affected by a product recall event in the last five years
- 78% manage the risk by procuring insurance
- 77% experience recalls that had a financial impact of less than $30 million
- The largest recall costs came from business interruption and product disposal
Furthermore, consumers are paying more attention than ever. And while you may be painstakingly thorough in your own food safety and quality control processes, it’s important to consider the other organizations with which you partner across the supply chain.
The reasons for product removals and withdrawals range from contamination with a pathogen, such as E. coli, to a foreign object, such as metal, to a nutrient imbalance or undeclared allergens. But one thing is for sure: When your brand is involved in a removal or withdrawal event, it’s inconvenient at best—and permanently destructive at worst.
To ensure better outcomes, it’s important to institute a product removal strategy that corresponds with FDA guidelines. This way, in the likely event you face a product removal or market withdrawal situation, your organization will be prepared. In addition, establishing standard processes, open communication and transparency across your supply chain will help you - and the organizations you work with - make better decisions and reduce the risk associated with product removal events. In making the effort to perform your due diligence and ensuring your supply chain partners do so as well, you are not only protecting your brand, but also fostering a better, safer industry.
FoodLogiQ’s recent E-Book, “The Food Manufacturer’s Guide to Effective Product Removal Management,” details the key steps to take when responding to or executing a product removal, and discusses essential methods for establishing preventive processes and strategies. Download the guide to get started on crucial steps for reducing risk, resolving product removal events and implementing preventive strategies.
Tag(s):
Recall
Other posts you might be interested in
View All Posts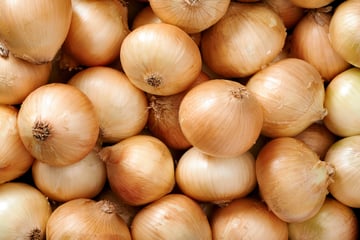
Recall
3 min read
| March 29, 2021
Recall Readiness: Lessons Learned and a Look Ahead
Read More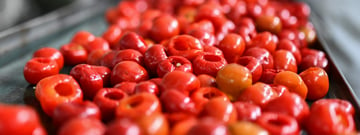
Food Safety
6 min read
| October 14, 2022
Modern Traceability Recordkeeping, FSMA 204, and the Supply Chain
Read More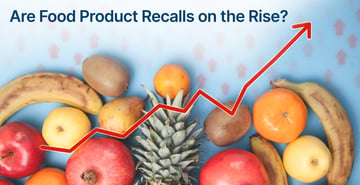
Food Industry
10 min read
| June 5, 2023