A food product recall can make or break your company. And unfortunately, they’re becoming more common. While recalls can happen for a number of reasons – from mislabeled ingredients or missed allergen declarations, to contaminated foods and illness outbreaks – consumer trust can easily be lost, and consumers are likely to avoid recalled brands for some time. As a result, the financial impact of food recalls can be massive. Depending on the size, scope, and cause of the recall, and your brand’s reaction, your organization could be paying upwards of $10 million in costs – perhaps even more for larger, high-profile recalls.
What exactly, though, do those costs entail? How can a batch of contaminated lettuce or shipment of granola bars with inaccurately labeled packaging, for example, create that much financial damage? Let’s explore a cost breakdown and how food companies can take preventative steps today.
The Complete Picture: Associated Recall Costs
Here are just a few of the potential costs associated with a food recall:
- Product and Supply Chain costs, including covering costs for retailers, distributors, and consumers affected as well as the cost of destroying or disposing of the recalled product.
- Investigation costs, including fees associated with lab testing for contamination, audit expenses, or expenses related to hiring a third-party to conduct an investigation.
- Legal costs, such as legal fees associated with the recall itself or for lawsuits and settlements from consumers harmed by the recalled product.
- Non-compliance costs, like fees for government fines or expenses related to conducting a Food and Drug Administration (FDA) or United States Department of Agriculture (USDA) audit.
- Crisis management costs, including fees for managing media or PR inquiries or hiring a crisis management firm.
- Lost revenue, from the recall itself and current (or future) lost sales, customers, or market share.
- Reputation damage, perhaps the most costly of them all, can include expenses incurred from trying to repair brand image and the cost of losing trust from loyal consumers.
The bottom line: food recalls can bring irreparable damage to your company, both in terms of financial loss and your brand’s image. In an increasingly complex and global food supply chain, it is critical for brands to keep food safety at top of mind; this includes taking preventative action to avoid food recalls.
Preventative Action for Food Recalls
In 2011, the FDA enacted the Food Safety and Modernization Act (FSMA) to shift the industry’s approach to food safety from reactive to proactive. In line with this mind of thinking, companies can – and should – be thinking of preventative measures to enact now to ensure a safer food supply chain. While food recalls are bound to happen, there are steps companies can take to help prevent them.
Have you been a part of a live recall? Without proper preparation, recall events can be stressful and challenging to navigate. Luckily, Trustwell is offering a unique opportunity to see a live (mock) recall happen in real-time with our recent online webinar. Tune in as we show how FoodLogiQ Recall can help companies navigate recalls and launch withdrawal notifications the moment they happen:
Watch Now!
Mastering Recall Response: Live Demo of FoodLogiQ Recall in Action
Five Proactive Recall Best Practices
While you can’t predict when a recall will occur, you can take proactive steps today to keep your team and company aligned with recall best practices. Here are some tips:
- Ensure traceability and visibility. True end-to-end supply chain traceability is invaluable for a company. The ability to identify the exact location of a product down to the batch-lot level at any point along your supply chain enables greater visibility – both for your company and for the consumer – and can provide you with complete visualization into your ingredients and products. This type of visibility also allows you to identify areas of risk along the supply chain (think: identifying a contamination incident before it gets to a customer) so that you implement a proactive approach to food safety.
- Prioritize supplier management. Building and maintaining strong relationships with your suppliers is an important factor in being able to prevent food product recalls. With frequent communication and check-ins, you are establishing a relationship of trust where you can set expectations, perform quality check-ins to identify potential areas of vulnerability for contamination, and rest assured that all stakeholders involved are taking necessary actions to prevent issues and respond rapidly to food recall.
- Properly label food products. Inaccurate labeling, such as those with undeclared allergens, is one of the most common reasons for a food recall, according to the FDA. Invest in tools or solutions, like Genesis Foods, that enable you to create government-compliant and accurate food labels that will help prevent a food recall due to mislabeling. Taking the time to make sure your products are labeled correctly and allergens are declared from the start helps prevent costly mistakes and potentially life-threatening scenarios down the line.
- Understand FDA regulations and guidelines. Ensuring food safety and quality is not just a suggestion; it is mandated by the government. As such, your company needs to be aware of current laws and regulations (both at a national and state level) to ensure your current processes, systems, and procedures are compliant with food safety standards. Food safety regulations are complex and can cover everything from types of recalls to recordkeeping and documentation guidance. It is crucial to understand these aspects of supply chain safety, but if you’re unsure where to start, there are regulatory experts that can help.
- Have a recall plan in place. Although a company can take a number of steps to incorporate preventative actions into their day-to-day operations to avoid a food product recall, there is still a chance that one may happen. With this in mind, it is critical to make sure your team knows the appropriate steps to take for a food recall. Once you’ve created a recall plan, you can train your staff by having mock recalls. Being able to act quickly and efficiently can help prevent additional costs, mitigate further damage to brand reputation, and overall minimize impact.
Food recalls are no doubt costly, but with a proactive approach, businesses can shut down a recall before it becomes too damaging. Plus, there’s technology that can help. Reach out to our team to learn more about government-compliant labeling software and enhanced traceability software. And don’t miss an opportunity to see a mock recall happen in real-time with Trustwell’s on-demand Mastering Recall Response webinar.
Other posts you might be interested in
View All Posts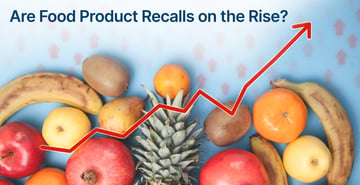
Food Industry
10 min read
| June 5, 2023
Are Food Recalls on the Rise? How to Avoid the Most Common Recalls
Read More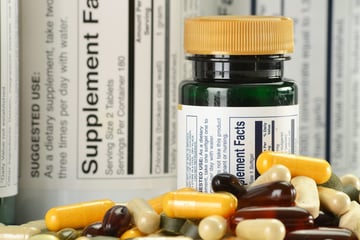
Food Labeling
12 min read
| March 15, 2023
How to Accurately Label Allergens On Dietary Supplement Facts Panels
Read More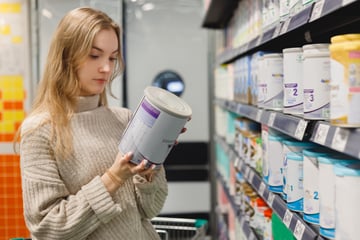
Food Industry
11 min read
| March 31, 2023