Capturing and storing the right supply chain event data can by leveraging tech-enabled traceability solutions not only helps companies visualize their entire supply chain but assists them achieve FSMA 204 compliance. Stitching together product and ingredient events at the batch-lot level can increase transparency, reduce time to locate tainted products, and minimize waste from withdrawals and product extractions.
Participants in the global food system need to speak the same language in order to reap these benefits. And, in recognition of this need, efforts are being made across the industry to build connections between stakeholders to enable interoperability, while standards bodies and regulators are also seeking to normalize food traceability data elements and practices. Understanding food traceability events is the key to understanding where the industry is headed in terms of supply chain modernization and transparency, specifically the evolution of two key concepts: Critical Tracking Events (CTEs) and Key Data Elements (KDEs).
What Are Critical Tracking Events (CTEs)?
Critical Tracking Events (CTEs) are defined as events recorded throughout the supply chain that are essential for achieving food traceability. Examples of Critical Tracking Events in the food industry include growing, receiving, creating, transforming, and shipping.
Further specifications for the types of information that must be captured can be dependent based on the type of CTE. The pieces of information, or attributes, required for each CTE are called Key Data Elements (KDEs). KDEs for food traceability events include data elements such as time, location, lot code, quantities or other units, business identification information, and more.
Critical Tracking Events and FDA FSMA 204 Regulations
With the finalization of FSMA Section 204, the landscape for food traceability and the requirements for recording Critical Tracking Events (CTEs) have been firmly established, marking a significant advancement in the regulatory oversight of food safety practices. As of the recent update, the Food and Drug Administration (FDA) has solidified its stance on the traceability requirements initially outlined in the FSMA Final Rule on Requirements for Additional Traceability Records for Certain Foods. This final rule provides a comprehensive framework for the capture and storage of information pertaining to CTEs, ensuring a more transparent and secure food supply chain.
Critical Tracking Events, as defined under the finalized FSMA 204 regulations, encompass crucial points in the food supply chain where critical information must be recorded to ensure the traceability of food products. These events include activities such as harvesting, cooling, initial packing, first land-based receiver, shipping, receiving, and transformation. The final rule elaborates on the specific recordkeeping requirements for each CTE, ensuring that businesses across the food supply chain have clear guidelines on how to comply with these regulations.
Leveraging Technology for Enhanced Traceability
Technology can be leveraged to capture, store, and share digitized data elements of Critical Tracking Events. Traceability technologies include IoT devices, scanning technologies, RFID, automated systems, and supply chain transparency software. Together, traceability technologies create an ecosystem that ensures visibility and compliance and enables business innovation. Trustwell's FoodLogiQ Traceability software provides an essential hub for farm-to-fork event data.
With FoodLogiQ Traceability you can:
- Import event data through your method of choice: Empower your team to provide event data in the most convenient format for your supply chain. Connect supports EDI 856 over AS2, CSV through FTP or web uploads, manual entry, RFID, API, or scanning with the Connect mobile application.
- Deliver accurate traceability data to the C-Suite and consumers: Use custom attributes to specify exactly what information needs to be collected from your suppliers and distributors. Empower your team to make data-driven decisions based on supply chain traceability.
- Comply with FSMA 204: Quickly export events to an FSMA 204-compliant Electronic Sortable Spreadsheet. Exports to this format will download a zip file containing the relevant event, location, and product information required by the FDA for FSMA 204.
Get Started
With over 190 million CTEs processed through our system, Trustwell provides the precision, accuracy, and expertise required to navigate the complexities of FSMA 204 compliance. Our dedicated team is ready to guide you through implementing a robust traceability system that not only meets regulatory requirements but also drives business value through enhanced supply chain visibility and consumer trust.
Contact Trustwell today to learn more about leveraging our FoodLogiQ Traceability software for seamless FSMA 204 compliance and transforming your supply chain challenges into opportunities for growth and innovation.
Other posts you might be interested in
View All Posts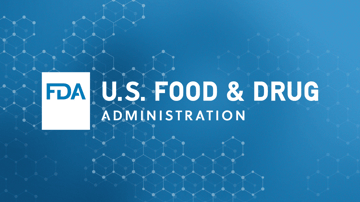
Traceability
6 min read
| January 29, 2021
Gearing up for Traceability 2.0 with FSMA
Read More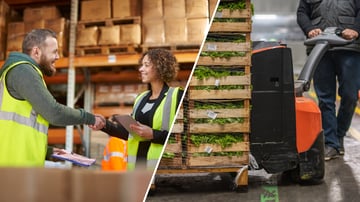
Food Industry
16 min read
| December 8, 2023
FSMA 204 Tools for Success: Creating a Food Traceability Plan
Read More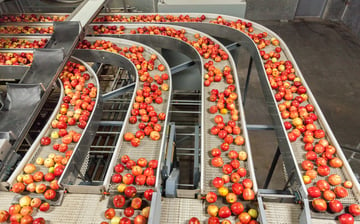
Trustwell News
6 min read
| December 17, 2021