When a business must issue a food recall, a proper recall plan must be already in place to minimize its effects. This will allow the company to mitigate more significant problems by reducing the time necessary to act. Whether the recall is self-initiated or by FDA mandate, it’s critical to have a guidebook for any potential scenario. Below, we outline ten critical steps to consider when going through a food recall.
Identification and Scope
Step 1: Gather details of the suspected tainted product.
Once a potential product issue has been identified, food safety professionals must gather details regarding the suspected tainted product. This includes the product name, shipment size, production dates in question, lot number, packaging, and relevant pictures.
Without a robust food safety optimization platform, this process is entirely manual and will vary depending on the initial scope.
Step 2: Determine the impact.
Once the pertinent details have been gathered, the Recall Manager or Recall Team must determine the severity of the issue. This includes determining whether the problem is a Class I, II, III, or quality withdrawal.
Step 3: Identify the scope.
The recall or food safety team must then determine the true scope of the recall event. This includes the impacted locations, suppliers, potential customers, and warehouses or storage facilities.
Scope identification can take hours, perhaps days, depending on the depth and breadth. Without the right technology, a business can improperly scope the recall. This, in turn, increases waste and costs or misses potentially tainted products. Software tools like FoodLogiQ Traceability can identify the scope of a recall within minutes.
Communication and Response
Step 4: Determine the appropriate response.
Once the scope has been established, a regulatory agency or supplier primarily drives the next course of action. Their role falls into one of five actions: remove the product from circulation, destroy it if necessary, hold and wait for further information, return to the supplier, or replenish with a modified product.
Step 5: Communicate and coordinate with stakeholders.
Communication is perhaps one of the more critical steps in the process, as it can dictate the success of the recall event. In this step, impacted constituents within the supply chain must be notified. These include but are not limited to individual locations, customers, suppliers, legal, regulatory agencies, PR, and senior leadership.
Utilizing pre-written templates allows for automated communication, follow-up, and escalation, if necessary, to all impacted stakeholders. Depending on the scope, consistent communication can require a full-time software resource for the duration of the recall.
Step 6: Verify the product defect.
Depending on the decided response and communication, businesses must verify the product defect. This might include a product having the wrong packaging, undeclared allergens, or any biological, chemical, or physical hazards. This is done to more accurately determine the full extent of the issue.
Documentation, Reporting, and Close Out
Step 7: Gather and analyze recall data for reporting.
Reporting is essential for better understanding the event and mitigating risk. It’s critical to know the following details: quantity in the supply chain, quantity found, quantity pulled, destroyed, or held, time and personnel responsible for pulling and destroying, and replenishment needed.
It's important for the data and analysis to be collected consistently regardless of recall size and duration. Tools like the FoodLogiQ Recall solution provide real-time data and analysis via a live dashboard.
Step 8: Monitor the effectiveness of the recall.
With the recall plan underway, it’s critical that businesses continue to monitor and manage ongoing recall performance. It’s also important to consistently communicate results to both internal and external stakeholders.
Step 9: Ensure quality and process improvements to prevent future events.
These improvements are mostly determined by a committee with a comprehensive understanding of the recall and surrounding circumstances. They must communicate the improvements to the proper teams and ensure that they are completed.
Step 10: Close the recall and ensure robust documentation of the event.
A host of internal and external factors mandate the need for robust documentation of any recall event. This can mitigate risk in the event of investigations or lawsuits.
Proper documentation may require a software partner's automation to ensure accurate and prompt reports.
Wrapping Up
Ultimately, food recalls are common and should be planned properly. This means businesses should have recall plans already defined so that any issues can be mitigated quickly and effectively. Remember that working with industry-leading partners like FoodLogiQ can save time, allocate resources efficiently, and consistently generate critical data and analysis.
Want to see FoodLogiQ Recall in action? Watch our recent on-demand webinar, Mastering Recall Response, to learn just how streamlined the recall process can be when you have a unified solution for communication, escalation, monitoring, and tracking a recall event.
Tag(s):
Recall
Other posts you might be interested in
View All Posts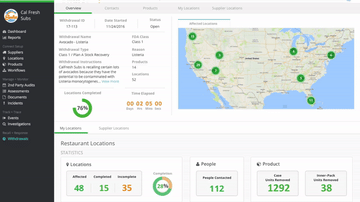
Food Industry
6 min read
| May 18, 2017
FoodLogiQ Disrupts the Food Industry with Market’s First Real-Time Recall Management Solution
Read More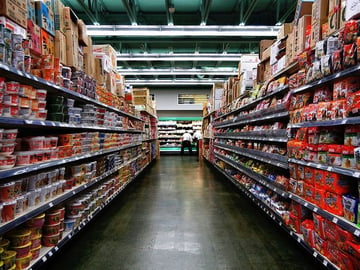
Food Safety
8 min read
| February 1, 2017
When it Comes to Food Recalls, Prevention is Key
Read More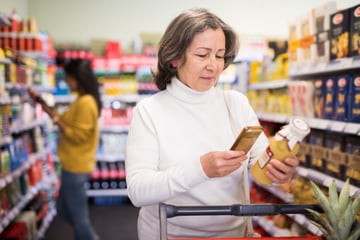
Food Industry
8 min read
| June 13, 2023