Consumers have access to more information than ever in today's interconnected world. With this comes an increased focus on transparency for businesses across the supply chain and fulfillment methods, as well as sourcing.
Accessibility to this information is especially true in the food industry, as the growing demand for food transparency pushes companies to focus on not only abiding by FDA regulations but going above and beyond– and having the evidence to prove it.
Today's consumers want food brands and retailers to share more than just ingredient lists and nutrition facts. They seek credible information about manufacturing practices, ingredient sourcing, company sustainability efforts, and more. Shoppers expect full disclosure of such details as a key indicator of transparency, which is critical to earning trust and loyalty. Claims made on the packaging of being "organic," "antibiotic-free," or "GMO-free," etc., will quickly lose value if manufacturers cannot back up these claims with evidence and timelines.
Food brands, however, shouldn't just prioritize transparency for the sole purpose of gaining a competitive advantage but should work to ensure all products travel safely through the supply chain and meet regulatory compliance.
Regulation and Recall Responsiveness
Food safety continues to be on the mind of manufacturers and consumers alike, especially in the wake of recent major food product recalls involving peanut butter, dairy products, fruits and vegetables, and dietary supplements. In standard recall procedures, the FDA or manufacturer releases details about the contaminated product, ranging from brands to batch numbers.
The balance of foodborne epidemiology and when to go public will always pose challenges to manufacturers. If a contaminated food product is missed by proper production and testing, the problem is usually not detected until enough people become ill. And the time between consumption, illness, investigation, and recall can stretch for weeks or months, depending on the number of sick people and the jurisdictions that encompass the outbreak.
The resolution to such delicate and time-critical issues is increased traceability and transparency from food industry supply chains. By continuously monitoring their supply chain, companies can significantly improve the speed of recall resolution. Factors like batch numbers, farms of origin, expiration dates, and other important data points can be identified when a recall is required. With greater supply chain transparency and detail, potentially contaminated food can be identified more quickly and accurately and with greater specificity to mitigate negative impacts.
Complete supply chain visibility and end-to-end traceability will provide the precision needed to take swift and decisive action during a crisis. Furthermore, implementing a robust, end-to-end traceability solution will allow you to view and act on real-time data as the product moves through your supply chain. The FDA proposed Section 204 of the Food Safety Modernization Act (FSMA) rule for additional traceability requirements will further escalate the need for automation technologies and supply chain visibility to help comply with these new regulations.
Ensure Quality Through Transparency
Quality control is embedded into every step of the food industry, from sourcing to fulfillment and distribution. Assurance of food safety and quality is essential to the success of a food company and is enabled by traceability processes. Food production facilities must track quality control procedures such as ingredient specifications, approved supplier lists, manufacturing procedures, and in-process records to ensure food is consistently held to a high standard of safety and quality.
FDA inspections and additional audits require manufacturers to ensure their tracking data is up to date and readily available. Transparency into these processes and quality assessments can help companies not only to catch and prevent errors but also to give consumers insight into the accuracy behind quality standard claims. Suppose a food manufacturer can provide quality assurance documentation throughout every step of the food fulfillment process. In that case, customers will feel more confident in the safety and quality of the food produced and therefore create a better connection to the brand.
Foodborne illness surveillance is a complex task and will always come with challenges. In pursuit of faster processes, accuracy and safety must be the ultimate goal. Transparency is the key for companies trying to avoid quality or contamination issues, keep consumers safe, and preserve brand reputation.
Building Trust for Customer Loyalty
Transparency and a willingness to share information are vital to gaining consumer trust through guaranteed food safety and quality. Trust translates into customer loyalty and creates value for the customer and the company regarding reputation and accountability. Consumers expect transparency and traceability from food companies in all ways, especially in prevention and reaction methods to food and beverage recalls. Companies that embrace transparent marketing through labeling, online mission statements, and access to information about their transparency initiatives are also being embraced by the public.
As consumers demand transparency, food companies have an opportunity to educate consumers, communicate health credentials, ensure quality products, and maintain customer loyalty.
Related:
Other posts you might be interested in
View All Posts
Food Industry
4 min read
| August 9, 2017
At the Crossroads of Food Safety and Consumer Transparency
Read More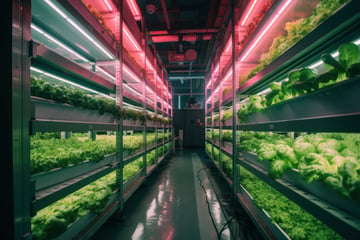
Supplier Compliance
9 min read
| August 24, 2023
Lessons Learned from Major U.S. Recalls & How Traceability Tech Turns the Tide
Read More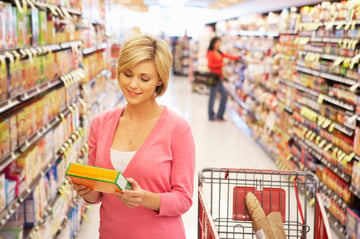
Food Industry
5 min read
| July 27, 2018