From putting consumers at risk, to damaging the reputation of your brand, product recalls can result in some significant (and costly) consequences. For decades, companies have been doing all they can to avoid being caught up in a recall of their products with traceability tech leading the way.
But what have we learned from some of the most high-profile food recalls in recent history, and how can food companies apply these lessons? Whether it’s increasing transparency, being proactive or building stronger relationships with suppliers, history has shown us that there are several ways, in addition to adding in technology, that food companies can be always ahead of recalls and withdrawals.
Tech-enabled solutions are creating a huge benefit for companies to get ahead of consumer worries and recall incidents. And while grocers, restaurants and distributors look toward the future of tech, they can also look back to find out how they can improve their processes even more. Let’s look at some of the major tech enhancements that have occurred over the past couple decades and where the industry can go from here.
Three Major Lessons from U.S. Recalls & How to Apply Them
There is no doubt food safety regulations have gone through some tremendous changes over the past 20 years, and the technology to help companies stay compliant and improve safety is no different. Each major publicized recall event has left ripple effects across the industry, resulting in better methods to trace contaminants back to their source, as well as a number of changes to lab testing, reporting, and quality management.
Lesson 1: Establish Strong Supplier Relationships and Enforce Accountability
In 2006, an outbreak of E. coli O157:H7 infections were found connected to leafy greens and spinach sold in various parts of the United States. Multiple brands issued voluntary recalls of their products, and the FDA advised consumers to avoid eating spinach altogether until they could identify the origin.
At the time, tech-enabled traceability wasn’t widely available to many of those affected by the recall. Farms and food sellers often used paper records of sales and shipments, which led to the FDA being unable to identify which farm or area was causing the outbreak. While this was a troubling time for the food industry, it also kicked off a new era in food safety – one in which traceability tech became the answer to build transparency across the supply chain.
- Regulatory Impacts: This and other recall events led to the creation of the Food Safety Modernization Act (FSMA), which passed into law in 2010. FSMA established stronger produce safety standards and mandatory prevention controls, which encouraged many facilities to establish better recordkeeping systems for their food products. Additionally, FSMA established mandatory inspections for high-risk foods and testing by accredited laboratories. After the legislation was passed, companies had some time to comply and update their recordkeeping systems, laboratory practices, and food safety standards.
- The Lesson: Recall incidents often trace back to issues within the supply chain, highlighting the significance of strong supplier relationships and accountability. Food businesses should establish comprehensive supplier management best practices, including regular audits and inspections, to ensure that suppliers stay current on certification and adhere to stringent food safety standards, like having a food safety plan in place or paying attention to food labeling guidelines. Transparent communication and collaboration with suppliers fosters a shared commitment to product safety, reducing the likelihood of contaminated ingredients entering the production process.
Lesson 2: Prioritize Transparent Communication and Traceability Standards
As technology has improved after the initial outbreaks of the early 2000’s, companies were finding it easier to trace outbreaks back to their source. For example, the 2018 outbreak of E. coli infections linked to romaine lettuce was eventually traced to lettuce grown in Northern and Central California. The exact cause of contamination – whether through irrigation water, animal intrusion, or other factors – wasn’t conclusively determined, but the expansive recall resulted in the largest recall of romaine lettuce to date.
However, while regulators were able to identify the general area at the center of the outbreak, the entire process took much longer than anticipated and specific farms were unable to be identified further. As a result, the FDA used lessons from this outbreak to improve traceability initiatives further and support the industry in implementing FSMA’s Produce Safety Rule.
- Regulatory Impacts: At the end of 2022, the FDA released their final rule for Section 204 of FSMA, establishing enhanced food traceability recordkeeping guidelines for the industry. The ruling creates a tighter timeline for handing over records and improving how food and related tracking events are recorded across the supply chain. While the final rule does allow for paper records, it also establishes strict guidelines for storing records and encourages farms and supply chain partners in establishing tech-enabled solutions that utilize a standard language for traceability data. Furthermore, food companies impacted by the legislation are required to create and implement a traceability plan, among other guidelines.
- The Lesson: Effective traceability systems and clear communication channels are vital during recalls. The ability to quickly and accurately trace the source of contamination is crucial in identifying and isolating affected products, minimizing the scope of recalls, and protecting consumers. Additionally, establishing a prompt and transparent communication plan to notify consumers and stakeholders in a timely manner can help maintain consumer trust and further mitigate the impact of recalls.
Lesson 3: Be Proactive
In 2020, the infant formula recall made waves across the industry. Again, the FDA was able to trace back along the supply chain to the source of the outbreak and issue a recall. However, the recall combined with supply chain disruptions due to the pandemic, destabilized a critical market for vulnerable newborns.
If this situation taught us anything, it is that across the supply chain, producers need to remain always ahead and vigilant with plans on what to do when issues arise. Technology has become a beacon for getting prepared for recalls just like this. In fact, FoodLogiQ Recall offers mock scenarios and practice recalls as a way for users to see exactly how a recall would be implemented if it were ever needed.
- Regulatory Impacts: While the FDA made some significant changes in how their Human Foods department is structured, the department also issued a series of steps to help get the baby formula market back on track with pre-pandemic levels. And they recognized that at the heart of the infant formula shortage there was one critical element missing: a proactive approach to protecting the industry from a shortage of critical supplies. With the guidelines released, the FDA suggested increased inspections of formula manufacturers, mandatory reporting of potential shortages, and guidance for firms outside the U.S. market looking to sell and be compliant with U.S. infant formula guidelines.
- The Lesson: Perhaps the most important lesson of all: be proactive in your approach to food safety. Take any and all necessary steps to prevent a food product recall from happening in the first place. This includes understanding the latest regulatory guidelines and protocols, establishing food safety plans so that your team is knowledgeable about what to do, and investing in the right technology solutions, like Trustwell’s FoodLogiQ Recall, to help you prepare and respond rapidly in the event of a food product recall.
Building a Safer Future for Food Today
While these major recalls represent just a few of the most significant food safety incidents of the past few decades, they also represent an opportunity for all of us in the food industry to learn from and improve processes and relationships to prevent further outbreaks. Technology is large part of how companies can get even better and do their part to keep America’s food supply safe.
Is your team prepared for a recall? Watch our latest on-demand webinar to learn some essential tips on recall responsiveness, and for businesses looking to be proactive in their approach to preventing food product recalls, reach out to us – our team can help.
Tag(s):
Supplier Compliance
,
Recall
,
Food Safety
,
Traceability
,
Industry Regulations
,
Trustwell Software
,
Food Recalls
,
FSMA
Other posts you might be interested in
View All Posts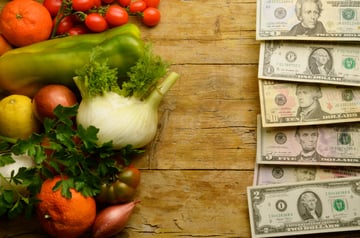
Product Formulation
10 min read
| February 24, 2023
The Price of Safety: Understanding the True Cost of a Food Recall
Read More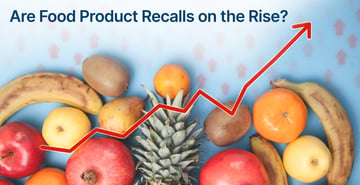
Food Industry
10 min read
| June 5, 2023
Are Food Recalls on the Rise? How to Avoid the Most Common Recalls
Read More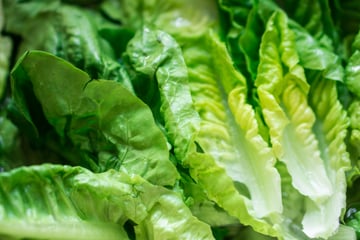
Supplier Compliance
8 min read
| May 31, 2018